The new tank of Comano Terme designed by Eng. David Marchiori
For the construction of the new Comano Terme (TN) tank designed by Eng. David Marchiori, Arbloc company from Salgareda (TV) has studied and created a technical solution with a non-ordinary shape in high density polystyrene, to provide an innovative design and a high level of functionality.
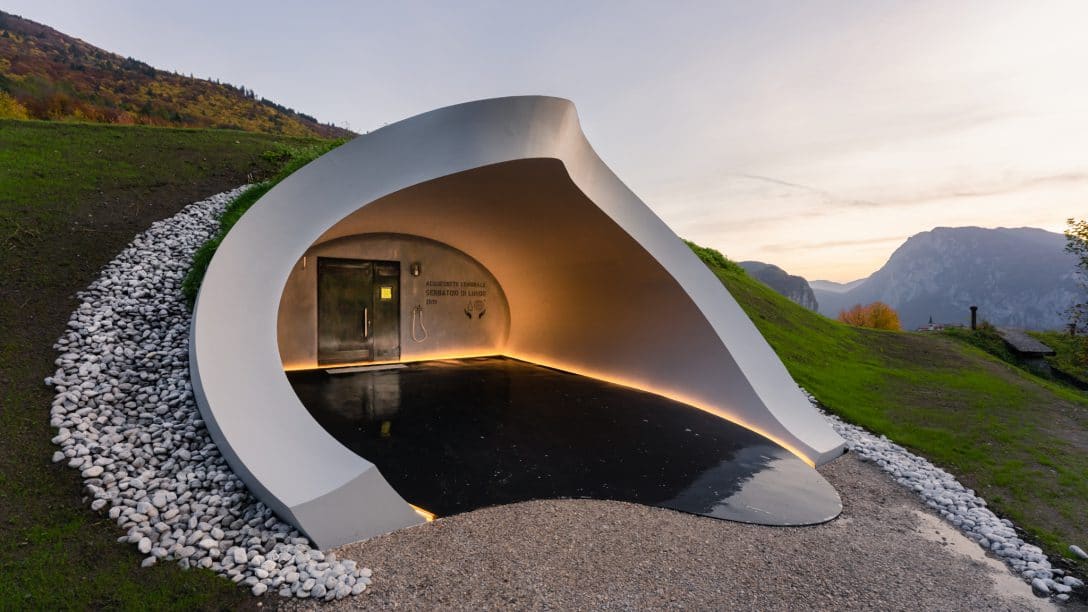
Solving a water supply problem for a small mountain community without affecting the surrounding naturalistic context, combining functionality and respect for the landscape: this is the prerequisite for the design of the new drinking water tank in Lundo, a hamlet of the Municipality of Comano Terme.
The pipeline that brings water from the source to the reservoir was built in 1970 across an entire valley. It fed a small underground tank which, unable to meet the need of water reserves for the populations of Lomaso, was replaced by a new tank. The project was entrusted to Eng. David Marchiori of Comano Terme, who also supervised the construction.
The new work is a box-shaped concrete structure consisting of two cylindrical tanks with a diameter of 12 meters and about 5 meters deep, divided into two levels: on the lower floor there are the delivery and discharge pipes and the ultraviolet irradiation drinking water plants, on the upper floor, instead, the supply pipes of the tank arrive and can be accessed through a tunnel.
The entire structure is covered by a semi-cylindrical concrete vault, 50 cm thick. The cover cap has a minimum height at the opposite ends of the tanks and a maximum height between the two tanks themselves. Two series of circular columns, resting on the edge of the tanks, support the roof slab.
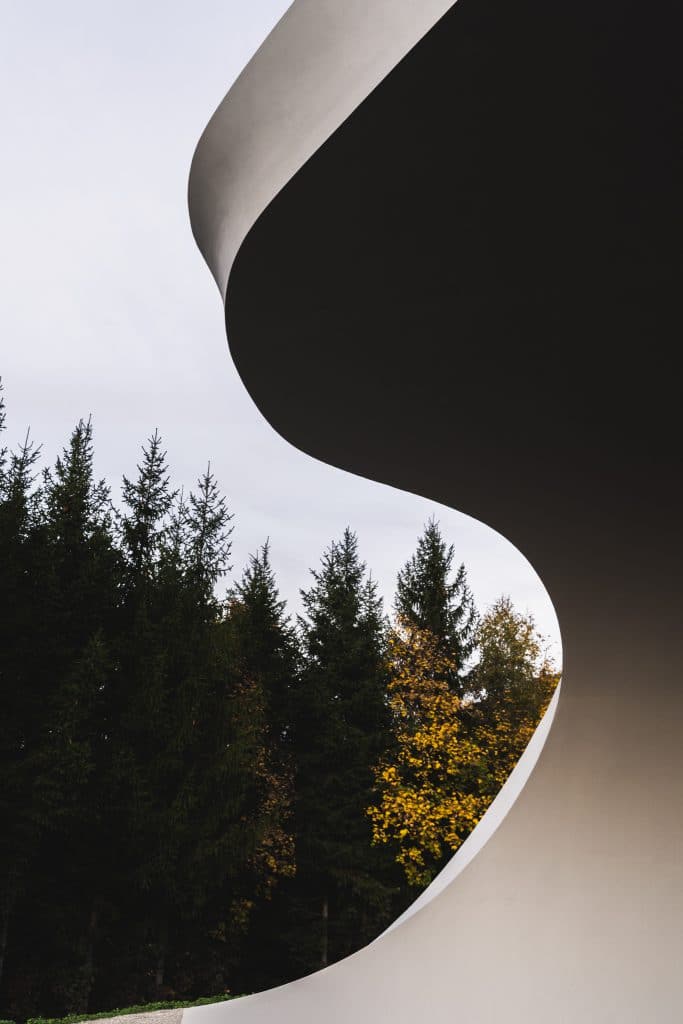
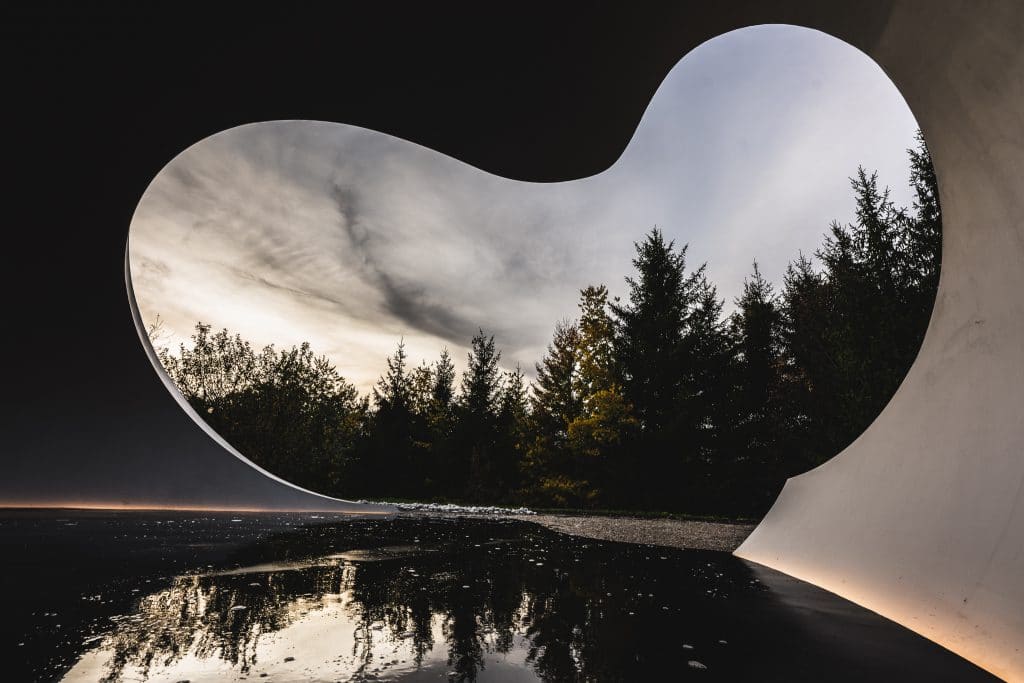
Eight hundred cubic meters of concrete of different types created the work, from the mixture added with waterproofing to the self-compacting conglomerate. The concrete was supplied by the company Onorati S.r.l. which dealt with the selection of aggregate, mix design and laboratory assistance for site checks on concrete carried out by the construction manager.
Seven hundred kilograms of steel make up the box armor which has been designed to be as thin and widespread as possible, generally maintaining a mesh not exceeding 15x15cm and diameters between 10 and 14 mm. The rebend connections were made partly with rubber joints and castings with sandy aggregate (0-15mm), and partly with the “Penetron” technology.
These are the numbers of a work of quite relevant dimensions for the natural context of the eastern edge of Lundo, a small fraction of the municipality of Comano Terme.
The lowest possible environmental impact on the surrounding valley in accordance with the landscape protection commissions led to the complete burial of the work, with the exception of the small access tunnel, which had to be particularly cared for from an aesthetic point of view. In fact, this passage has been entrusted with the task of being the only element visible to the visitor, the explicit sign of the presence of the tank and of the new work for the territory and its inhabitants. The choice of a cylindrical shape for the cover, as well as structural factors and better management of the water condensate, responds to the purpose of connecting the building with the lively surrounding morphology, which lies between the Alpine countryside and the wood, between rural and unspoiled nature. The design inspiration created a shape that could recall the morphology of the ice, the quintessential natural freshwater reserve, and that was at the same time functional and organic. The contoured shape of the access tunnel, first drawn by hand and then with software, needed to find a construction system that faithfully respected what was designed.
Design, construction and use of the Arbloc formwork
Arbloc, a manufacturer of coated polystyrene formwork, has taken on the burden of studying and making an unusual shaped formwork, which was developed from the three-dimensional drawing provided. The 3D development was fundamental for identifying and correcting some aspects related to carpentry.
The formwork was made with high density polystyrene with compressive strength of 60KN/m2. The coating with reinforced syform resin made it possible to have a surface suitable to be walked on and to resist impacts during iron working.
The tunnel (a 6 meters wide arch with a height of 3.28 meters and a length of 4.60 meters) has been broken down into several elements, each one meter long.
The Arbloc technical office, in agreement with the executing company, has divided the formwork design into ten elements for the construction of the shaped part of the entrance with the curves provided for in the project. The formwork was assembled on site with the coordination of the designer with instructions issued by the manufacturer, and direct supervision of Arbloc technicians that provided the necessary advice and precautions. The holes for the passage of the tie rods were made directly during the production of the formwork in order to facilitate the carpentry work.
Finally, the casting of self-compacting concrete, made through a hole drilled in the upper part of the formwork, allowed to fully enhance the manufacturing and obtain a work corresponding to the design features.
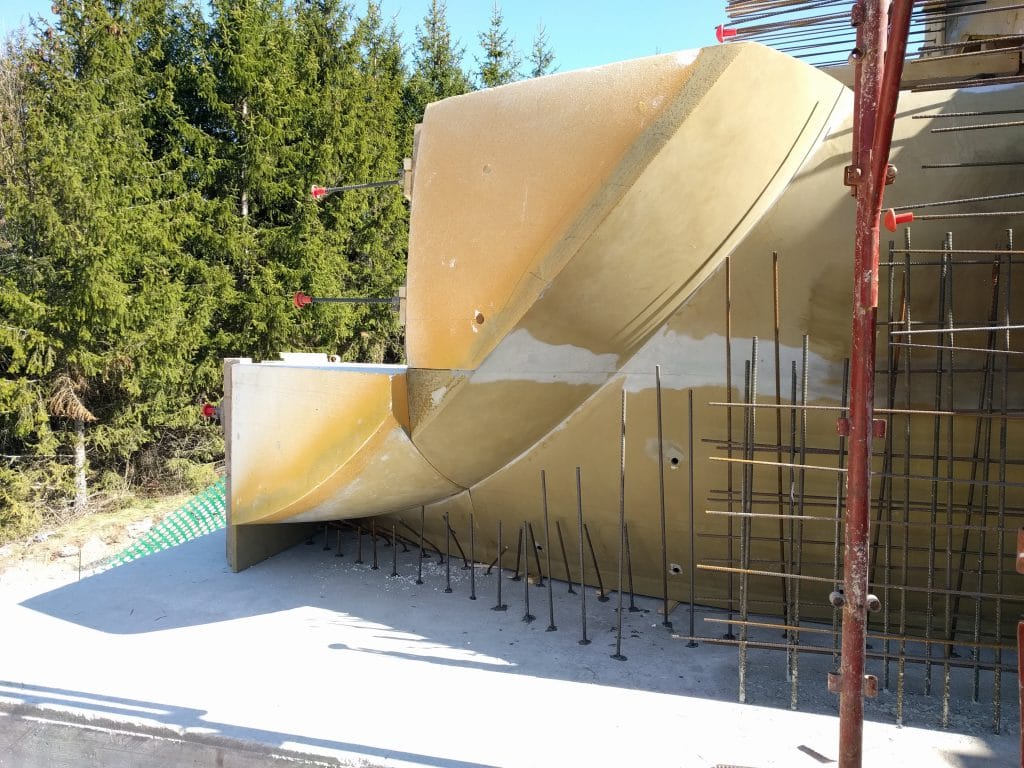
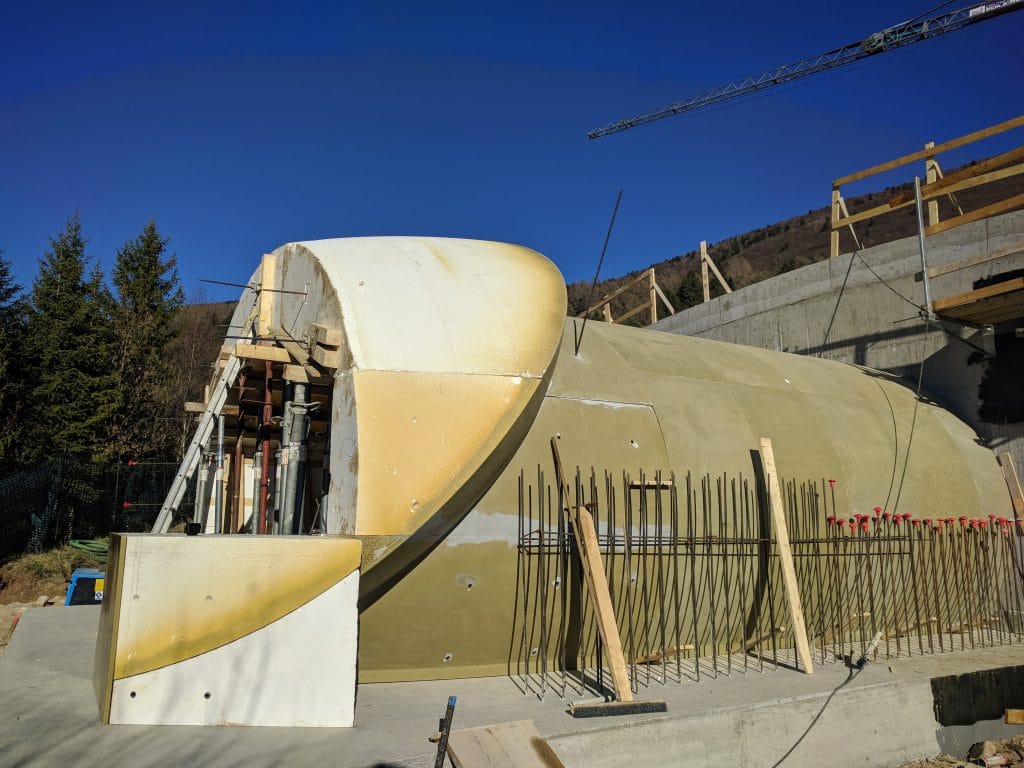
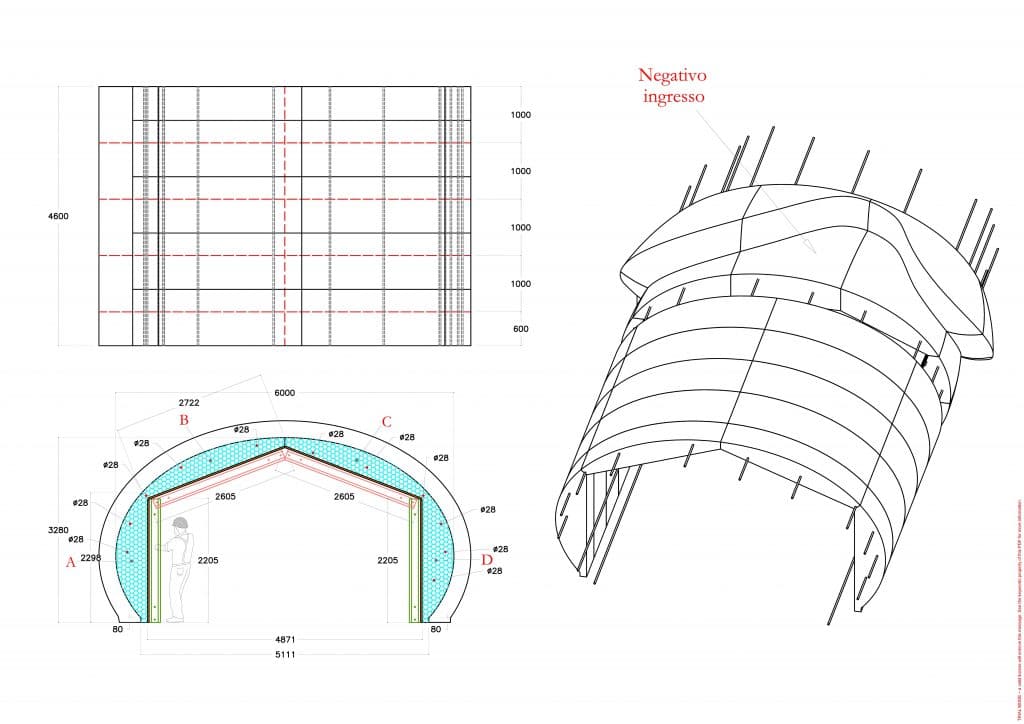
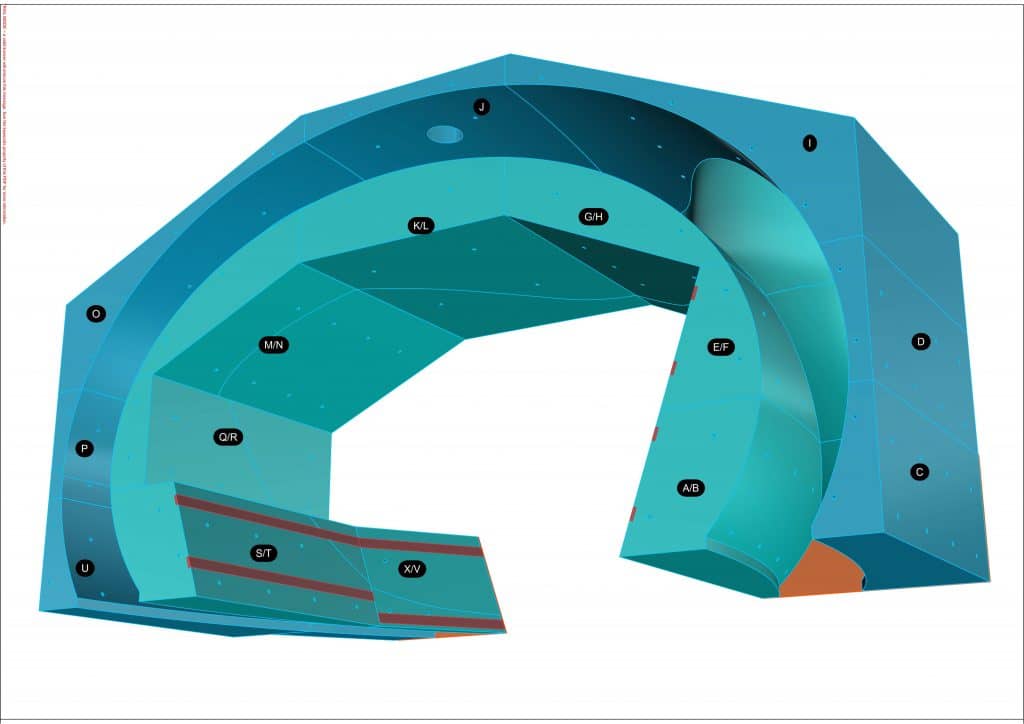
Project and construction supervision: Eng. David Marchiori www.wrconsult.eu
Shaped formwork: Arbloc s.r.l. www.arbloc.com
Contributions to the realization:
- Structural consultancy: Eng. Pierangelo Lombardi, Malcesine (VR)
- Contracting company: Pavoni S.p.A., Vobarno (BS)
- Sub-contractor company: Impresa costruzioni Salvadori Felice, Bagolino (BS)
- Concrete and mix design: Onorati s.r.l., www.onoraticls.it
- Waterproofing: “Penetron” tramite Bindo s.a.s., www.bindo.eu
- Photographs by: Samuele Guetti